Pennine Pneumatic Services Ltd (PPS) recently helped a plastic recycling firm to reduce its compressed air energy usage. In the plastics industry, this customer has very high targets to meet for carbon footprint reduction.
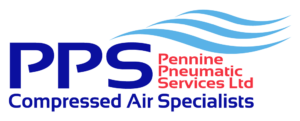
Pennine Pneumatic Services Logo
Its application uses a significant amount of electricity to melt plastic and, compressed air is critical to the manufacturing process.
The first part of the recommendations focused on a leak detection survey. Using an ultrasonic acoustic detector, the PPS engineer found 16 leaks. All leaks were tagged and the customer was provided with a full report showing the details of the leakage, including energy and monetary savings. For this customer, PPS supplied the parts needed to fix all the leaks.
In total the customer spent £809.35 to detect and repair air leaks, in order to save £15,356.97 per year due. The savings are based on a price of £0.12/kWh.
This site had an estimated leakage rate of 74CFM and the compressor it was running was capable of 150CFM. By fixing the leaks they have saved money, reduced their carbon footprint and increased capacity.